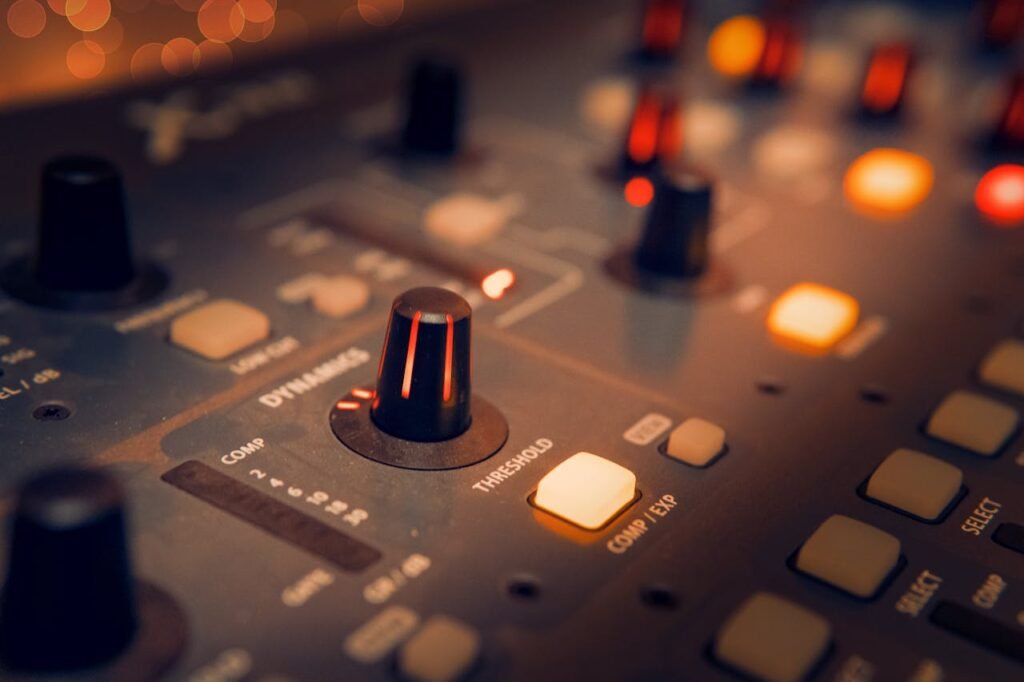
Innovative Tools for Tank Level Control
Efficient liquid level control is a critical element in any industrial operation. From chemical plants to food processing facilities, proper tank level management ensures both safety and efficiency. But with evolving technological advancements, traditional manual methods no longer suffice. Innovative tools for tank level control are paving the way for more accurate, automated, and cost-effective solutions that streamline industrial operations while minimizing risks.
If you’re an industrial engineer, plant manager, or maintenance personnel, leveraging these tools can enhance accuracy and efficiency across your facility. This blog dives deep into the latest tank level control technologies and how they’re revolutionizing industrial processes.
Why Tank Level Control Matters
Tank level control serves as the backbone of numerous industries, ranging from oil refineries to wastewater management systems. Monitoring liquid levels in storage tanks prevents overflow, ensures proper supply management, protects equipment, and reduces downtime. Without proper tools, the potential for operator error increases, resulting in costly damage or even safety hazards.
Modern solutions are bridging these gaps by offering advanced monitoring systems that reduce human error and ensure dependable accuracy.
Understanding the Challenges of Traditional Methods
Traditional tank level control methods often rely on manual observation or basic float systems. While these may seem cost-effective, they carry inherent shortcomings, including inaccurate readings, susceptibility to wear-and-tear, and lack of remote monitoring.
Key Challenges of Traditional Solutions Include:
- Manual Intervention: Constant human observation can lead to lapses and errors.
- Limited Accuracy: Mechanical failures can result in incorrect level readings that compromise safety and efficiency.
- Lack of Real-Time Data: Without automated tools, operators lose access to immediate and actionable insights.
These limitations create inefficiencies in operations, making it clear that advanced tools are necessary for optimal performance in today’s fast-paced industrial environments.
Modern Solutions in Tank Level Control
Advancements in tank level measurement technologies now offer automation, enhanced accuracy, and remote control functionality. Here are some innovative tools addressing the needs of modern industries.
1. Radar Level Sensors
Radar level sensors have emerged as a game-changing technology. Utilizing microwave signals, these sensors measure liquid levels with unrivaled accuracy, even in extreme conditions.
Advantages of Radar Level Sensors:
- Highly accurate, regardless of environmental changes.
- Non-contact measurement reduces maintenance needs.
- Performs well with volatile chemicals or dense liquids.
For example, food processing plants use radar sensors to measure liquid ingredients like oil or syrup while maintaining a sterile environment due to their non-contact capabilities.
2. Ultrasonic Level Sensors
Ultrasonic sensors use sound waves to determine liquid levels. They are highly reliable in areas where cleanliness and safety are paramount.
Benefits of Ultrasonic Sensors:
- Suitable for open tanks and reservoirs.
- Cost-effective for non-critical applications.
- Readily available with integration into remote monitoring systems.
Facilities like water treatment plants frequently implement ultrasonic sensors for straightforward, consistent level measurement across multiple tanks.
3. Magnetostrictive Sensors
Magnetostrictive sensors offer another innovative leap, specifically for applications requiring extreme precision, such as in pharmaceuticals or oil and gas industries.
Magnetostrictive Sensor Features:
- Enhanced accuracy for critical levels.
- Withstands harsh conditions like extreme heat or chemical exposure.
- Requires minimal calibration over time for consistency.
This tool is invaluable for plant managers seeking high sensitivity without compromising reliability.
4. Bluetooth-Enabled Smart Monitors
Bluetooth-enabled smart level controllers are rapidly gaining traction for small-scale industrial operations. These devices connect to mobile apps to provide real-time monitoring on-the-go.
Advantages of Bluetooth Controllers:
- Convenient remote monitoring from anywhere.
- Ideal for small-scale tanks in industries like beverages or farming.
- Reduces the need for on-site labor.
These tools bring insightful data to operators’ fingertips, allowing for faster responses to any developing issues.
5. Advanced Process Control Systems (APG)
Advanced Process Control Systems (APG) integrate seamlessly with your facility’s existing infrastructure, optimizing tank-level operations holistically. These systems leverage predictive algorithms to provide insights and reduce downtime.
For example, APG systems can predict liquid demand trends, enabling automated refills and reducing the risk of downtime due to supply exhaustion. Their flexibility ensures wide performance improvements across multiple tank setups, benefitting maintenance personnel and plant managers alike.
Benefits of Innovative Tank Level Control Tools
By integrating advanced tank level control tools, industrial facilities can expect numerous benefits that outweigh the investment costs.
Reduced Downtime
Automated systems reduce downtime during regular operations or even unexpected occurrences like leaks, enabling faster decision-making and task execution.
Enhanced Safety
Non-contact sensors, in particular, ensure workers’ safety by minimizing exposure to hazardous liquids.
Cost Efficiency
Fewer breakdowns, improved resource management, and reduced waste translate to long-term savings.
Data-Driven Insights
Modern tools provide critical real-time data about tank levels, improving overall decision-making and operational clarity.
The Future of Tank Level Control
The next steps in tank level control are all about connectivity and advanced analytics. The rise of the IIoT (Industrial Internet of Things) means that tank systems will become increasingly connected, enabling complete facility integration and smarter automation.
Plant managers will soon see a world where tanks not just measure levels but also predict future consumption trends, optimizing the entire supply chain.
Closing Thoughts
For industrial engineers, maintenance teams, and plant managers, innovative tank level control tools like radar sensors, ultrasonic devices, and APG systems deliver unmatched accuracy, simplicity, and efficiency. These advanced systems are essential for driving safer, smarter, and more cost-efficient operations.
Are you ready to elevate your tank level control systems? Start by exploring what APG has to offer in providing seamless and robust solutions.
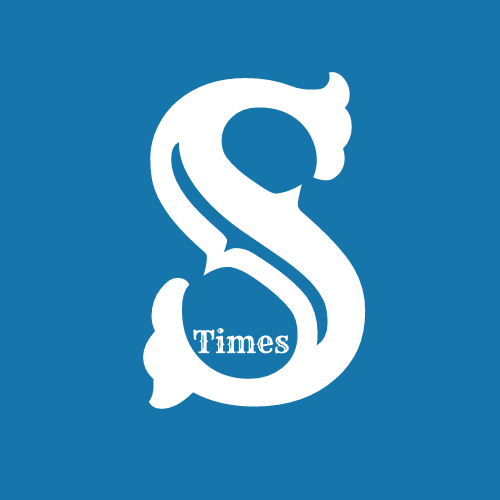
We create powerful, insightful content that fuels the minds of entrepreneurs and business owners, inspiring them to innovate, grow, and succeed.