
Are There Customizable Options for Conveyor Rollers
Rolling conveyors are essential in various industries and processes for efficient material handling. In manufacturing, they streamline assembly lines, moving parts between workstations. Warehousing and distribution centers use them for sorting, packing, and shipping goods. The food and beverage industry relies on rolling conveyors for processing and packaging products. In the automotive sector, they facilitate the transport of heavy components. Airports utilize them for baggage handling systems. Additionally, rolling conveyors are vital in mining operations for transporting extracted materials. Overall, they enhance productivity, reduce manual labor, and ensure the smooth flow of materials in diverse industrial settings.
Customizable options for conveyor rollers can greatly enhance the efficiency of rolling conveyors in various industries. Many manufacturers offer a range of modifications, including size, material, and coating, to meet specific operational requirements. This flexibility allows businesses to optimize their conveyor systems for speed, load capacity, and environmental factors.
Choosing the right customizable features can lead to improved performance and reduced maintenance costs. Whether it’s adjusting the roller diameter or selecting a specific material for durability, these options provide valuable solutions tailored to individual needs.
The availability of customization for conveyor rollers opens doors to significant operational advantages. With the right configuration, companies can ensure their conveyance systems are both effective and cost-efficient, adapting to the unique demands of their workflows.
Overview of Conveyor Roller Technologies
Conveyor roller technologies play a crucial role in the efficiency of rolling conveyors. The materials used and the design types significantly influence the performance, durability, and adaptability of these systems.
Materials and Composition
The materials used in conveyor rollers include various plastics, metals, and composite materials. Common choices are UHMW (Ultra High Molecular Weight Polyethylene) for its low friction and wear resistance, and steel for its strength and durability.
Key materials include:
- Steel: Offers high load capacity and resistance to wear.
- Aluminum: Lightweight and corrosion-resistant, suitable for lighter applications.
- Plastic: Ideal for applications requiring lower weight and noise reduction.
The composition also affects the roller’s ability to operate in different environments, including exposure to chemicals or extreme temperatures. Employing the right material ensures optimal performance and longevity in diverse operational conditions.
Roller Design Types
Roller design types vary widely, affecting how materials are conveyed and handled. Key design types include:
- Idler Rollers: Used to support the conveyor belt and help it maintain tension.
- Drive Rollers: These rollers propel the conveyor belt, providing the necessary movement.
- Return Rollers: Function to guide the belt back to the start of the conveyor system.
Each design type has specific applications, such as enhancing efficiency, reducing wear, or improving load handling. Customizing roller designs can optimize performance for unique conveyor systems, ensuring they meet specific operational needs.
Customization Aspects of Conveyor Rollers
Conveyor rollers can be tailored to meet specific operational requirements. By focusing on dimensions, surface treatments, and performance features, individuals can enhance the effectiveness of their rolling conveyors.
Dimensional Variations
Customization begins with dimensions. Conveyor rollers are available in various lengths, diameters, and widths to accommodate diverse material handling needs. Standard sizes may not suit all applications, thus manufacturers often provide options for:
- Diameter Adjustments: Typically ranging from 1 inch to 8 inches, larger diameters can support heavier loads.
- Length Customization: Rollers can be produced in lengths from a few inches to several feet, allowing for compatibility with varying conveyor systems.
- Weight Capacity: Each dimension correlates with a specific load capacity, so careful selection is crucial.
These variations ensure that rollers fit seamlessly into existing conveyor systems, enhancing operational efficiency.
Surface Treatment Options
The surface treatment of conveyor rollers significantly affects their performance and longevity. Various treatments are available to enhance durability, grip, and resistance to wear:
- Coating Options: Rollers can be coated with materials such as rubber or urethane, improving grip and abrasion resistance.
- Corrosion Resistance: Treatments like galvanized coatings or stainless steel surfaces are available for environments exposed to moisture or chemicals.
- Textured Finishes: Texturing the surface increases friction, which can be beneficial for moving goods without slippage.
Selecting the right surface treatment promotes optimal performance and extends the lifespan of the rollers.
Performance Features
Addressing specific operational challenges may require unique performance features in conveyor rollers. Customization can involve:
- Brake Rollers: These rollers incorporate braking systems to control speed and enhance safety.
- Drive Rollers: Integrated with motors, these rollers actively drive the conveyor system.
- Noise Reduction: Features such as cushioned materials can reduce operational noise, creating a quieter work environment.
Tailoring these features ensures that conveyor rollers align closely with industry-specific requirements, improving overall efficiency in rolling conveyors.
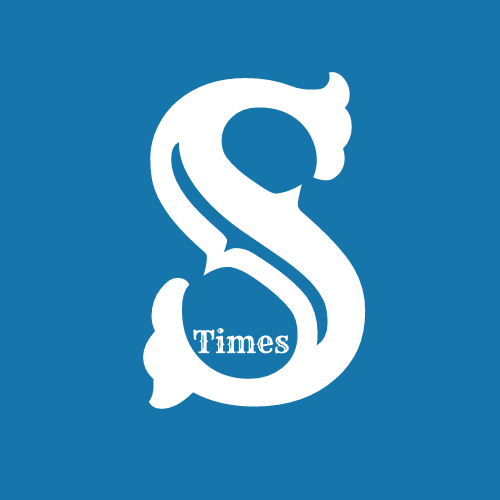
We create powerful, insightful content that fuels the minds of entrepreneurs and business owners, inspiring them to innovate, grow, and succeed.