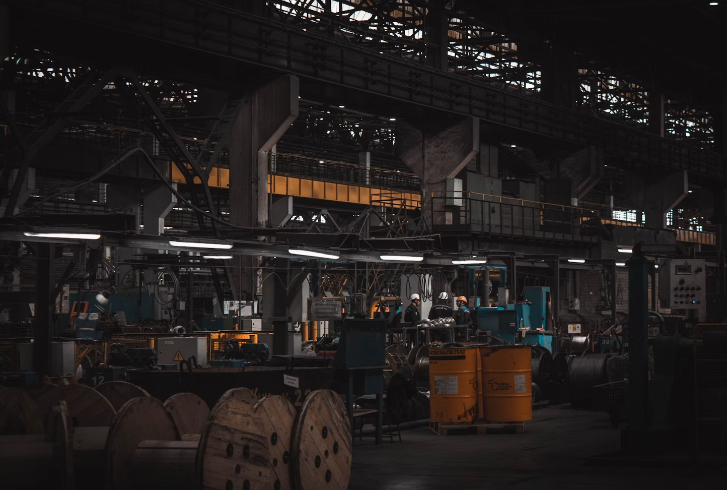
The Hidden Complexity of Calculating Manufacturing Costs
Manufacturing is often thought of in terms of physical labor, machines, and materials, but beneath the surface lies a world of intricate calculations. Every product that rolls off a production line carries with it a set of costs that go far beyond the materials used to build it. These costs are the result of layered accounting, resource allocation, and estimations that must align with real-world variables. Understanding how to calculate these manufacturing costs with accuracy is critical for pricing, profitability, and competitiveness in any industry. Still, grasping the depth of the process demands more than plugging numbers into a spreadsheet; it requires a structured, nuanced approach.
Understanding the Formula Behind Manufacturing Costs
Any effort to quantify manufacturing expenses must begin with a solid grasp of the formula. The total manufacturing cost formula consists of three core elements: direct materials, direct labor, and manufacturing overhead. Each of these components brings its layer of complexity. Direct materials include the raw inputs that physically become part of the finished product. Direct labor refers to wages paid to workers who are directly involved in the production. Manufacturing overhead encompasses all other associated costs, such as utilities, equipment depreciation, factory rent, and quality control. When applying this formula, precision in data collection becomes the foundation. It’s not enough to simply track material purchases or wage expenses. Costs have to be traced accurately to the right product lines, batches, or shifts. Overhead, especially, can be tricky to allocate. Choosing the wrong basis for allocation, be it machine hours, labor hours, or square footage, can distort product profitability. The formula may look simple at first glance, but its accuracy hinges on the quality of the inputs and the relevance of the allocation methods used.
Breaking Down Direct Material Costs
Direct material costs seem easy to measure; what was purchased and used in production is counted. But timing and waste complicate things. Material pricing can fluctuate weekly, and not all materials ordered are used immediately. Some may be damaged, stolen, or miscounted. Manufacturers must distinguish between materials on hand and those consumed in a given production cycle.
Inventory systems play a significant role here. Companies often use methods like FIFO (first-in, first-out) or LIFO (last-in, first-out) to track material usage, but these methods affect the value assigned to material consumption and, by extension, the total manufacturing cost. Then there’s spoilage, shrinkage, and return rates, all of which must be factored into the real cost of materials. Getting this wrong inflates or undercuts margins and misleads operational planning.
The Subtleties of Direct Labor Calculation
Direct labor costs may appear straightforward: track the number of hours worked by employees on the production floor and multiply those hours by their hourly wage. At first glance, this method seems efficient. But when examined more closely, a range of nuances come into play that complicate the accuracy of labor cost calculations. Only the time workers spend directly involved in manufacturing counts toward direct labor. This excludes time spent in training, attending meetings, completing paperwork, or performing non-production duties, which are often miscategorized. Misclassifying these hours inflates direct labor figures and distorts product cost structures.
The financial side brings further complications. Workers are rarely paid just their base hourly wage. Overtime pay, bonuses, holiday premiums, and shift differentials all contribute to the final cost. These adjustments must be accounted for, and not doing so can lead to underestimating labor expenses. Beyond wages, companies incur additional labor-related costs such as payroll taxes, health insurance contributions, retirement benefits, and paid leave. Each of these factors contributes to the total labor burden, which needs to be allocated correctly to individual products.
Unpacking Manufacturing Overhead
Of all the components, manufacturing overhead is the most ambiguous. This catch-all category includes everything from factory lighting to machine maintenance to supervisory salaries. What makes overhead difficult to manage is its indirect nature. These costs don’t neatly attach themselves to one product or process; they float above the floor, shared across operations.
Allocating overhead begins with choosing an allocation base. Labor hours work for labor-intensive operations, while machine hours make sense in automated environments. But what if a factory has both? Hybrid costing models are sometimes used, blending several allocation metrics to more closely reflect reality. Then there’s the distinction between fixed and variable overhead. Rent, insurance, and salaries are fixed; utility bills and maintenance costs may vary. Ignoring these distinctions leads to misleading cost estimations and poor budgeting decisions.
Hidden Costs and Their Impact
Other elements affect manufacturing costs but often remain hidden in plain sight. Waste, rework, and downtime silently chip away at margins. Scrap material, defective units, and idle machinery create costs that aren’t always captured by standard accounting entries. Tracking and attributing these losses require continuous monitoring and detailed reporting systems.
Then comes indirect labor and support functions. Janitors, supervisors, quality inspectors, and maintenance workers all support production but don’t directly touch the product. Their wages, often lumped into overhead, can distort cost figures if overhead allocation isn’t carefully calibrated. These hidden layers introduce variance between expected and actual costs, which in turn complicates forecasting and pricing strategies.
Technology and Automation in Cost Tracking
Digital tools have changed the way companies track and calculate manufacturing costs. Enterprise Resource Planning (ERP) systems and Manufacturing Execution Systems (MES) automate data collection, integrate departments, and provide real-time insights. These systems reduce manual errors and help companies fine-tune their costing strategies.
Yet, technology is only as effective as the rules it’s built on. Automated systems rely on assumptions and parameters set by humans. If these rules are flawed, say, an incorrect allocation method or outdated labor rate, the system will produce misleading outputs. That’s why regular audits, system recalibrations, and human oversight remain indispensable, even in highly digitized environments.
Calculating manufacturing costs is not a task to be glossed over. It demands attention to detail, rigorous systems, and continuous improvement. Missteps in tracking materials, labor, or indirect expenses ripple across the organization, influencing pricing, profitability, and strategic planning.
What appears to be a simple equation is anything but. Beneath its surface lies a complex web of variables that must be understood and managed with care. For manufacturers who aim to stay competitive and profitable, mastering this complexity isn’t optional; it’s foundational.
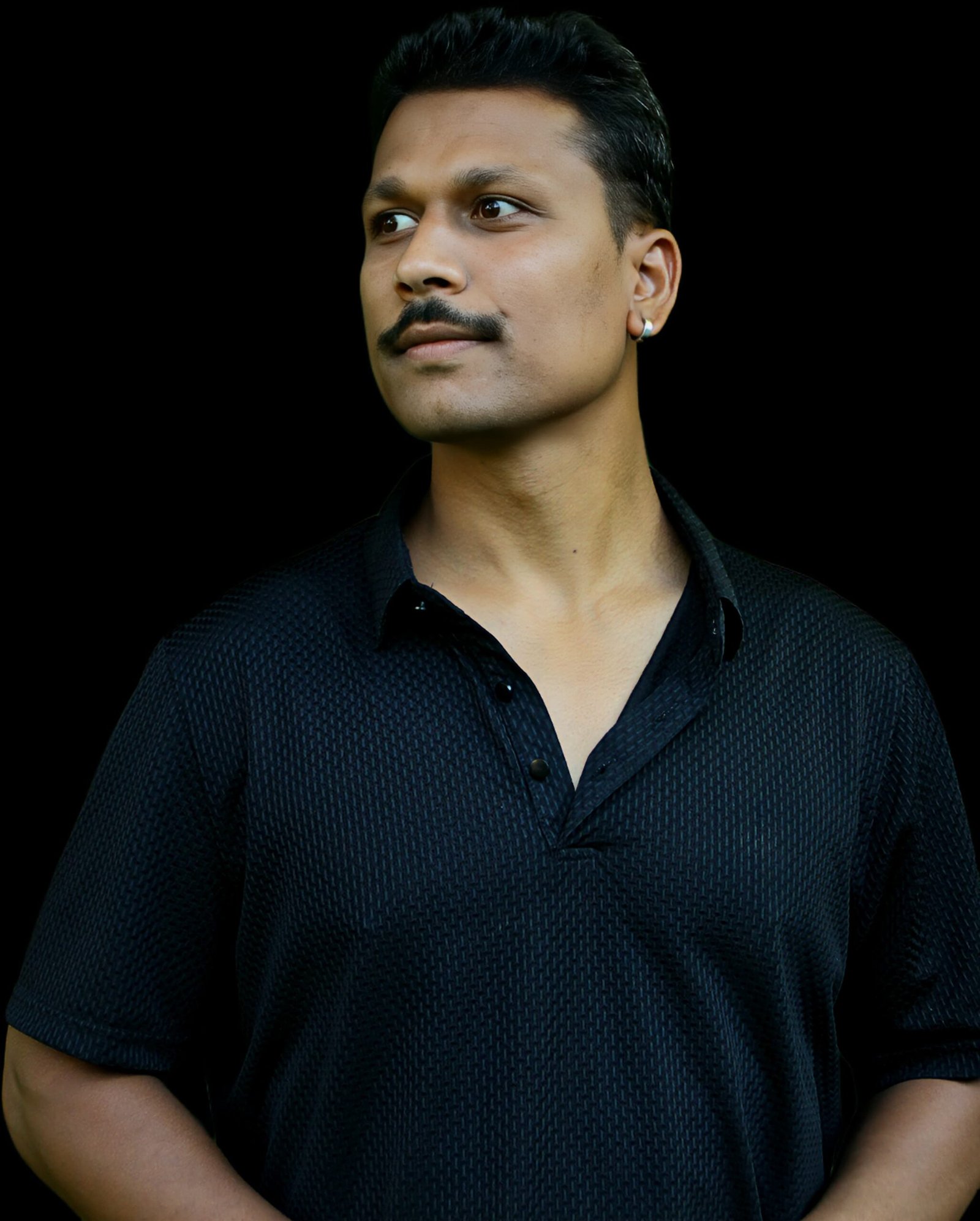
Sujan Pariyar is an internationally accomplished writer and entrepreneur, with his work featured in various renowned international magazines. Known for his innovative ideas and compelling storytelling, Sujan continues to inspire and engage audiences around the world.