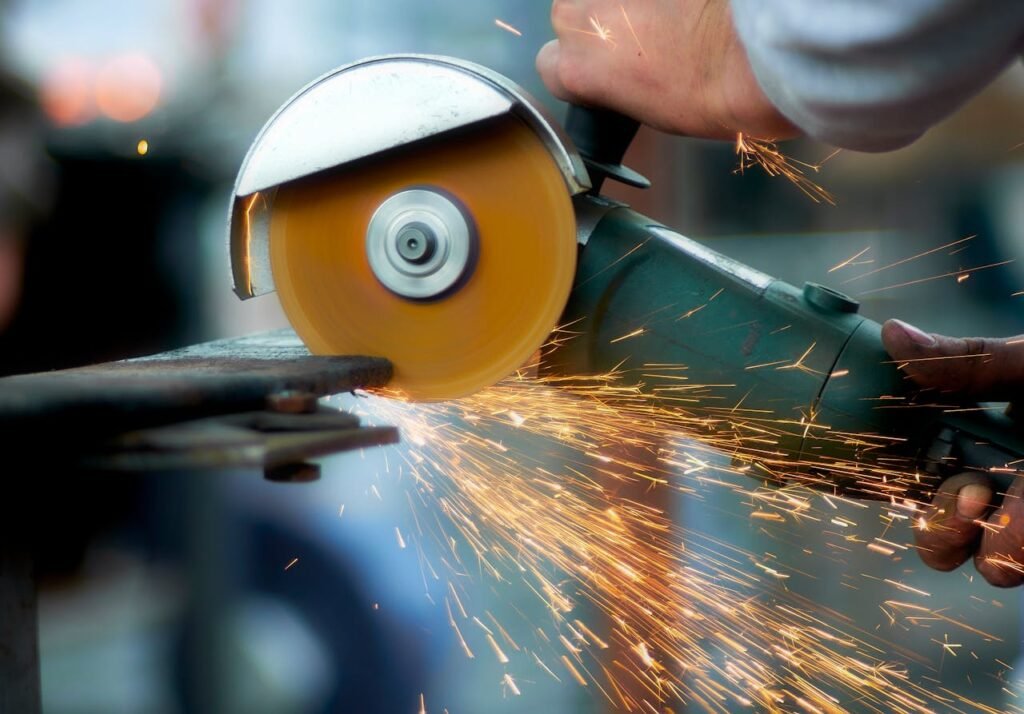
Best Practices for Using Abrasive Wheels in Industrial Settings
Working with abrasive wheels can be risky if safety isn’t a priority. These tools are powerful and versatile but can quickly turn dangerous if mishandled. Hazards like flying debris, sudden wheel breakage and excessive noise are common in industrial settings.
Without the proper know-how, accidents can happen in seconds. That’s why safe practices, adequate training and well-maintained tools are essential. Explore and learn about the essentials of working safely with abrasive wheels.
Understanding Abrasive Wheels and Their Applications
Abrasive wheels come in many shapes and sizes. They’re designed to grind, cut or polish a variety of materials. Each wheel type is made for specific jobs. Some are for heavy-duty cutting, while others handle fine detailing. Using the right wheel for the task makes a world of difference.
Common Types of Abrasive Wheels
- Cut-off wheels: Perfect for slicing through metal or concrete.
- Grinding wheels: Ideal for removing material or smoothing rough surfaces.
- Flap discs: Great for polishing and finishing work.
- Diamond wheels: Built to tackle rigid materials like glass or stone.
Choosing the correct wheel isn’t just about efficiency. It’s also about safety. A mismatched wheel might overheat, break or underperform. Always check compatibility with your equipment and materials.
Pre-Use Inspections and Maintenance
Before starting any job, take a moment to inspect the equipment. A quick check can prevent big problems later.
- Visual Inspection: Look closely at the wheel. Are there cracks, chips or wear marks? If you notice any damage, don’t use it. Damaged wheels can shatter, sending debris flying at high speeds. Even minor flaws can lead to severe accidents.
- Testing for Cracks: Perform a simple “ring test” to detect hidden cracks. Lightly tap the wheel with a non-metallic item. A clear ringing sound indicates the wheel is intact. A dull thud? That means trouble. Replace it immediately.
- Proper Mounting: Secure the wheel tightly, but avoid over-tightening. A loose wheel can wobble, while an overly tightened one might crack under pressure. Balance is crucial to prevent vibration and ensure smooth operation.
- Routine Maintenance: Keep all equipment in top shape. Clean your tools routinely and store them in a dry, secure place. Maintenance isn’t just about extending lifespan—it’s about staying safe on the job.
Personal Protective Equipment (PPE) and Safe Work Practices
When using abrasive wheels, never skimp on protective gear. PPE is your first line of defence against flying sparks, debris and noise.
Essential PPE
- Safety goggles: This protects the eyes from dust and debris. Always wear protective eyewear, even for brief tasks.
- Gloves: Shield your hands from heat and sharp materials. Use snug-fitting gloves for better control.
- Hearing protection: Noise levels can damage hearing over time. Wear earmuffs or noise-cancelling headphones.
- Face shields: For heavy-duty tasks, combine goggles with a face shield for complete protection.
Creating a Safe Work Environment
Secure your workstation before starting. Loose tools or unstable surfaces can create hazards. Stand to the side when starting the machine—wheels can fail during the first moments of operation. Always maintain a firm grip and position yourself to avoid kickback.
Noise awareness online training can help you understand and mitigate hearing damage risks by educating you on noise pollution and how to avoid it in a convenient and flexible environment.
Proper positioning is also crucial. Don’t lean into the wheel or apply excessive pressure. Let the tool do the work. Rushing can lead to mistakes, which can lead to injuries.
Compliance with Safety Standards
To stay compliant with safety standards, management should encourage them to undertake safety training programmes to equip them with the practical knowledge to understand and deal with hazards. Workers should complete abrasive wheels training online or in person before ever touching a machine.
It covers everything from wheel selection to proper mounting techniques. It also emphasises hazard recognition. For example, workers learn how to identify a damaged wheel or an unstable machine. Industry regulations exist for a reason—to keep people safe. Make sure the team knows and follows these rules. Regular refresher courses help keep knowledge sharp.
Documentation matters, too. Keep records of training sessions, inspections and maintenance checks. This not only ensures compliance but also creates a culture of accountability.
Conclusion
Abrasive wheels are handy but equally dangerous. By following best practices, workers can stay safe while getting the job done efficiently.
Regular inspections, proper maintenance and the correct PPE are the first lines of defence. Choosing the right wheel for the task prevents accidents and boosts productivity. Training ensures everyone knows what they’re doing and why it matters.
Safety is an ongoing process that requires vigilance and commitment. By prioritising safety and efficiency, industrial settings can thrive—without unnecessary risks.
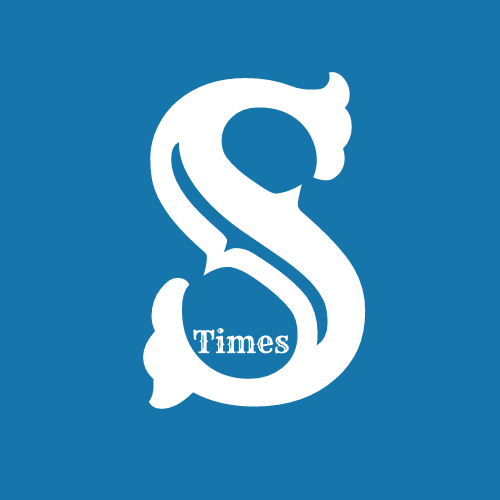
We create powerful, insightful content that fuels the minds of entrepreneurs and business owners, inspiring them to innovate, grow, and succeed.